Innovations in series
Matthias Meyering, Head of Product Management Electronics about new innovations from STOBER:
“Even more decisive than the sheer compactness of the SI6 is the omission of redundant supply units. The entire series of drive controllers is connected with a central supply module. The fuses and cabling for each individual axis are also dispensed with here. The drive controllers are connected with each other via Quick DC-Link modules. And by using double axis modules, unused power reserves of an axis can be used for other axes.”
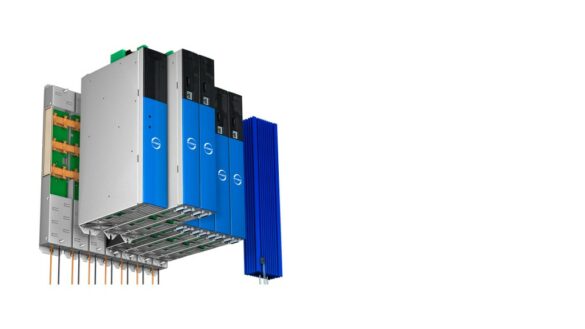
In this way, STOBER enables a significant reduction of space and costs. A realistic example: For a system with six axes, an 18 cm width is sufficient for the drive controller and supply module. The double axis modules can also be combined with stand-alone units from the STOBER SD6 series. No matter whether there are 4, 16 or 97 axes – the capacities are precisely dimensioned.
As regards acceleration, the STOBER SI6 drive controller has plenty to offer. In combination with the STOBER synchronous EZ401 servo motor, it accelerates from 0 to 3000 rpm in 10 ms. This can be used to precisely make changes to the speed. Decisive here: the interaction of the drive controller, servo motor and encoder. The SI6 processes encoder information up to 64 bit and calculates it without rounding (floating point arithmetic). This means the highest positioning accuracy with more than 33 million encoder resolution positions per revolution. Current encoder systems only deliver 37 bits. The SI6 is therefore prepared for future developments.
STOBER promises exceptionally simple installation. With just a few clicks and even less wiring: Using the new Quick DC-Link modules, the SI6 drive controllers can be connected with standard copper rail. These can be clicked in without tools.
In combination with Encoder communication via HIPERFACE DSL®, a common cable connection with the power connection is provided. The motor data is parametrized via an electronic motor nameplate that is available via HIPERFACE DSL® or EnDat® 2.2 digital.
For the safety concept, STOBER counts on the STO (”Safe Torque Off”) function that can be controlled via terminals as well as via Fail Safe over EtherCAT® (FSoE). The SI6 is categorized in the highest Performance Level e (cat. 4) according to EN 13849-1.
The Ethernet-based fieldbus systems EtherCAT® and PROFINET® are available in the STOBER SI6 drive controller as standard. With the device profile CiA® 402, the SI6 can be seamlessly integrated in Controller Based and Drive Based Solutions.
Rainer Wegener, Head of Management Center Sales, adds about the innovations: “STOBER is traditionally open for the interaction with components of other manufacturers. Naturally there are also no “language barriers” with the SI6. Thanks to Ethernet over EtherCAT®-protocol (EoE), Ethernet data is transported in the EtherCAT® system.”
Innovations in series: Without doubt, the SI6 looks elegant.
However an extremely robust design is concealed behind the delicate exterior. All components – from the stable, well shielded sheet steel housing to the motor connectors – exceed the reference values of industry standards by far. Even the inside is anything but small format: generously designed computer capacities, high-quality components, careful workmanship.
An overview of the technical features:
• Connection of several drive controllers via Quick DC-Link modules.
• Positioning accuracy (up to 37 bit) in conjunction with Heidenhain encoders EnDat® 2.2 digital or HIPERFACE DSL® (up to 20 bit) from SICK Stegmann. Depending on the encoder type, more than 33 million positions per revolution can be recorded.
• Simply assembly on the standard busbar 5 x 12 mm with Quick DC-Link.
• Electronic motor nameplate thanks to encoder systems HIPERFACE DSL® and EnDat® 2.2 digital.
• Safety: STO (”Safe Torque Off”) controlled via terminals or via Fail Safe over EtherCAT® (FSoE).
• Communication via Ethernet-based fieldbus systems such as EtherCAT and PROFINET.
• CIA 402 device profile for seamless integration in Controller Based and Drive Based Solutions.
About innovations and drive technology form STOBER: Our breadth of product means we have the product to meet all your application requirements.
Photo credits: STÖBER Antriebstechnik GmbH + Co. KG
Media contact, editorial / market overviews:
Please note the new persons responsible for PR & media:
STÖBER Antriebstechnik GmbH + Co. KG
Silvia Feder
Kieselbronner Str. 12
75177 Pforzheim │ Germany
Fon: +49 7231 582-1660
silvia.feder@stoeber.de
www.stoeber.de
Media:
STÖBER Antriebstechnik GmbH + Co. KG
Solveig Moll
Kieselbronner Str. 12
75177 Pforzheim │ Germany
Fon: +49 7231 582-1183
solveig.moll@stoeber.de
www.stoeber.de
Please send a specimen copy to our agency:
a1kommunikation Schweizer GmbH
Sarah Hartung
Project Management│Client Support
Oberdorfstr. 31A
70794 Filderstadt│Germany
Fon: +49 711 945 416-27
eva.neubert@a1kommunikation.de
www.a1kommunikation.de
Contact data for country-specific publication:
Germany:
STÖBER Antriebstechnik GmbH + Co. KG
Kieselbronner Str. 12
75177 Pforzheim
Fon: +49 7231 582-0
sales@stoeber.de
www.stoeber.de
Austria:
STÖBER Antriebstechnik GmbH
Hauptstraße 41a
4663 Laakirchen
Fon: +43 7613 7600-0
sales@stoeber.at
www.stoeber.at