Keeping Full Control
SOGA Gallenbach GmbH in Pforzheim, Germany, designs and develops special machines. One special machine is a multiple screwing unit that joins profile rails in reliable process operation for ROMA, one of the leading manufacturers of sun protection systems.
SOGA supplied a system with multiple mounting heads that reliably monitors screw depth and tightening torque. The drive technology needed for the axes of the heads, such as synchronous servo motors, planetary gearboxes, rack and pinion drives as well as drive controllers, all come from STOBER. The extremely compact and dynamic LeanMotor is also used. This new, encoderless STOBER motor class is an inexpensive and rugged alternative to the synchronous servo motor. As a partner in the project, STOBER also took care of the mechanical design and dimensioning.
“We offer our customers special developments they can use in production immediately after delivery,” says Managing Director Fabian Gallenbach. With his ten employees, SOGA Gallenbach GmbH in Pforzheim designs and develops special machines as well as solutions for fixture constructions and 3D printing and sells pneumatic components. The customers come from industries such as medical technology and aerospace engineering. “These industries have an especially high demand for precision,” Gallenbach says. And he knows a thing or two about precision. Gallenbach completed his trained at a Swiss watch manufacturer, where he learned to cut a micrometer in half. When founding the company, his goal was to take the precision he had learned and use it in machine building. This enables the company to meet customers’ constantly increasing requirements. “We hardly ever get simple requests anymore,” the managing director notes. When executing these demanding solutions, SOGA Gallenbach relies on the support of selected suppliers—or, better yet, partners. STÖBER Antriebstechnik GmbH + Co. KG, also headquartered in Pforzheim, has been one such partner for years.
Screwing without Rework
SOGA Gallenbach is in frequent contact with STOBER. For new projects, this makes it easier to immediately get down to the details. The drive specialists have helped the machine builder many times when they were looking for the right motor/gearbox combination—such as when developing a multi-screwing unit. The customer was ROMA, a leading manufacturer of special machines like sun protection systems such as roller shutters, venetian blinds and textile screens.
Previously, the medium-sized manufacturer drilled and screwed up to three aluminum or plastic profile rails using an automatically moving screwing unit with screw feed—without any monitoring measures. “Especially with wrought aluminum alloys, the drill screw frequently created chips between the screw head and profile rail,” says Gallenbach. A visible cap is placed on top of the screw, but because of the chips, the cap cannot be attached properly. The employees in production would repeatedly have to rework the piece manually. ROMA wanted to prevent this going forward.
“Over the past 15 years, we have developed more than 50 screwing units with torques from 0.4 to 200 newton meters,” says Gallenbach. “As a result, we made it possible for our customers to mount screws without needing the worker to manually retighten or perform rework.” ROMA wanted a solution for its special machines that also predrilled the profile rails to be processed, in lengths from 710 to 5,710 millimeters.
SOGA developed a screwing unit able to monitor different screwing depths and tightening torques for reliable processes. “We developed a strategy specifically for plastic screw connections in which our pneumatic screwdriver operates with pressure pulses,” Gallenbach explains the special machine. Plastic does not require the final torque to be any higher during the final tightening process than at any other point. This means that the unit has to be sensitive. The engineers also equipped the system with two drawers for loading the profile rails. As a result, the machine supplies profiles for processing either separately or synchronously. The components are manually inserted and clamped.
The Right Motor/Gear Unit Combination
In this development, it was important for SOGA Gallenbach to know that STOBER was on their side as an expert partner with a comprehensive product range. “The drawers move using two Y-axes in automatic operation,” says Guido Wittenauer, STOBER sales representative in charge of SOGA. For each drawer, the drive specialists delivered a PE series planetary gearbox with a belt and spindle drive combined with an EZ synchronous servo motor for this purpose.
The system feeds the screws automatically and screws them in pneumatically. The unit is also equipped with five mounting heads that move independently of each other in the X direction on a gear rack. “We equipped each head with a Z-axis and drilling axis,” says Wittenauer. STOBER provided ZVPE series rack and pinion drives as well as EZ synchronous servo motors for the X-axis. EZ-motors with spindle drive are also used for the Z-axis. To make sure that the five heads do not collide with each other on the gear rack, STOBER engineers implemented threefold collision protection: the controller monitors the positions in relation to each other, software limit switches were parameterized with the permitted travel range for each X-axis, and a mechanical safety switch is also located on each head.
The most compact motor possible with a low weight was to be installed for the drilling spindle of the special machine. “This allows us to keep the mass to be moved for the five axes low and thus achieve rapid positioning,” describes Wittenauer. In addition to drilling, countersinking also needed to be possible. This requires highly dynamic motor controls. STOBER supplied the LeanMotor (LM). This new development makes it possible to set speed and torque to any point, from a standstill to maximum speed, with full torque control—and the LM is completely encoderless. The solution is significantly lighter and more compact than an asynchronous drive with the same output and is more cost-efficient and more rugged than a servo drive. The motors reach the energy efficiency class IE5 with up to 96 percent efficiency. ROMA thus benefits from lower energy consumption and a long service life. Each head has three motors placed as close together as possible. “Since our LeanMotor functions without an encoder, only one standard power cable is necessary without any additional cores or shielding,” explains Wittenauer.
Reliable in the Background
STOBER combined the motors with new double-axis controllers from the SI6 series. This highly dynamic solution also makes challenging movements possible, working reliably in the background. STO (Safe Torque Off) and SS1 (Safe Stop 1) safety functions are integrated, certified in accordance with EN 13849-1 (PL e, cat. 4). “The drive controller has a width of only 45 millimeters and is designed as a multi-axis drive controller,” says Wittenauer. “A single drive controller can control up to two axes. Thanks to the serial connection of multiple controllers, the number of axes to be controlled can be scaled without limit.” Individual components can be installed practically: The patented Quick DC-Link modules can be simply clicked into the standard copper rails for power distribution and enable the simple installation of the drive controllers. STOBER also supports communication over the Ethernet-based PROFINET® fieldbus system.
As a partner, STOBER not only supplied the appropriate components for special machines. “We also took care of the mechanical design and dimensioning,” Wittenauer says. Support from the drive specialists began as early as the offer phase. Together, both sides discussed the critical points and worked them out step by step. “We developed the idea that the motor would form one unit for the X-axis with the gearbox and helical gear together in project conversations,” says Managing Director Gallenbach. The physical proximity naturally helped during the collaboration, as did good personal contact between the companies. This meant the axes could be easily parameterized on site. “The whole machine concept design is based on calculations for the motor technology, for example,” says Gallenbach. “An error in the design could endanger the entire automation system.” And ROMA? The manufacturer of sun protection systems can now operate with significantly more process reliability—and without doing any rework.
Captions:
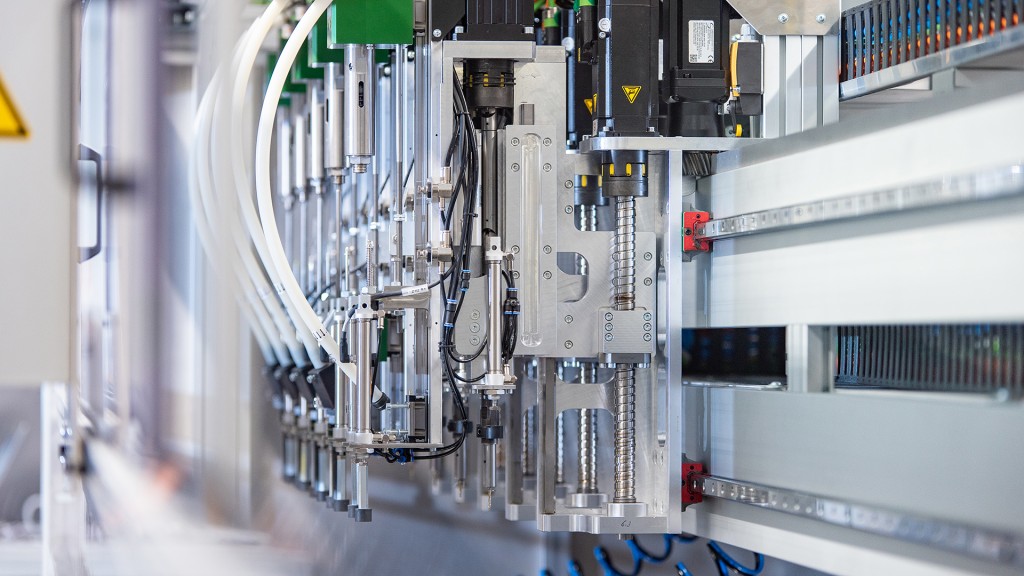
Photo credits: STÖBER Antriebstechnik GmbH + Co. KG
Media contact, editorial / market overviews:
Please note the new persons responsible for PR & media:
STÖBER Antriebstechnik GmbH + Co. KG
Silvia Feder
Kieselbronner Str. 12
75177 Pforzheim │ Germany
Fon: +49 7231 582-1660
silvia.feder@stoeber.de
www.stoeber.de
Media:
STÖBER Antriebstechnik GmbH + Co. KG
Solveig Moll
Kieselbronner Str. 12
75177 Pforzheim │ Germany
Fon: +49 7231 582-1183
solveig.moll@stoeber.de
www.stoeber.de
Please send a specimen copy to our agency:
a1kommunikation Schweizer GmbH
Sarah Hartung
Project Management│Client Support
Oberdorfstr. 31A
70794 Filderstadt│Germany
Fon: +49 711 945 416-27
eva.neubert@a1kommunikation.de
www.a1kommunikation.de
Contact data for country-specific publication:
Germany:
STÖBER Antriebstechnik GmbH + Co. KG
Kieselbronner Str. 12
75177 Pforzheim
Fon: +49 7231 582-0
sales@stoeber.de
www.stoeber.de
Austria:
STÖBER Antriebstechnik GmbH
Hauptstraße 41a
4663 Laakirchen
Fon: +43 7613 7600-0
sales@stoeber.at
www.stoeber.at